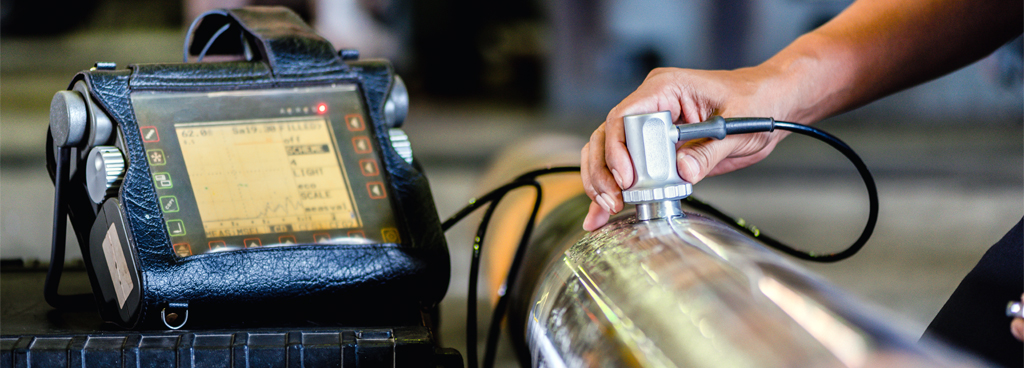
Services
Non-Destructive Testing Methods
Nondestructive testing has been defined as; applying a testing method to an object, part, component or system in order to evaluate it’s integrity without destroying the product’s future usefulness. Nondestructive inspection (NDI), nondestructive examination (NDE) or nondestructive testing (NDT) are terms generally used to identify the major inspection methods to perform evaluations or the application of the method to the item under inspection. Essentially, NDT is a function of material testing that evaluates a material or structure for uniformity, quality and serviceability and whether it will perform its intended function. In the beginning NDT was used primarily for process control and secondarily as quality control, subsequently the use of NDT became a means of meeting consumer demands for better products. It became a vital tool of modern engineering practice to achieve the required standards of quality in manufacturing which has instilled reputations in manufacturers adopting this methodology.
Nondestructive Testing can further be characterized by the purpose or intended use. In general, the purpose for NDT will fall into one of the following categories:
- Determination of material Properites
- Detection, characterization, locating and sizing of discontinuities or defects
- Determining the quality of manufacturing or fabrication of a component or structure to a code, specification or standard
- Verifying serviceability by inspecting components during use for deterioration or for failure prevention.
By detecting faulty material, thus preventing loss or failure of materials and loss of manufacturing time, nondestructive testing will increase productivity and proportionally provide economic gains to a manufacturer. Preventative maintenance inspection will provide increased serviceability of a component or part by monitoring and preventing failure. NDT reduces the potential for accidents, loss of life or property, decreases down time and reduces overall operating costs by detecting flaws prior to failure.
Radiography, Isotope, X-Ray, & Computed Radiography
Radiography is a method of nondestructive testing that utilizes radiation to penetrate an object and record images. The images can be recorded on a variety of different devices such as film or photosensitive paper.
Ultrasonics
Ultrasonic testing is a nondestructive method of detecting, locating, and evaluating internal discontinuities in metals and other materials.
Liquid Penetrant Testing
The liquid penetrant inspection method is based on the ability of certain types of liquids to enter into voids and crevices by capillary action and to remain there when the surface liquid is removed. Thus, liquid penetrant inspection, when done properly is a reliable and revealing method for detecting discontinuities open to the surface.
Eddy Current Testing
Eddy current testing is non-destructive testing (NDT) inspection method used for a variety of purposes including surface and subsurface flaw detection, cracks in bolt holes, material and coating thickness measurements, material identification and establishing the heat treatment condition of certain materials
Magnetic Particle
Magnetic particle inspection is a nondestructive method of detecting discontinuities in ferromagnetic materials. This method will detect surface discontinuities including those that are too fine to be seen with the un-aided eye; those that lie slightly below the surface; and, when special equipment is used, the more deeply seated discontinuities.
Visual Testing
For many types of welds and products, integrity is verified principally by visual examination. Even for welds that are to be examined by other NDT methods, visual inspection still constitutes an important part of practical quality control and quality assurance.
Welder Qualifications
Welder, welding operator, and tack welder qualification tests determine the ability of those tested to produce acceptably sound welds with the process, materials, and procedure called for in the test. Qualification tests are not intended to be used as a guide for welding during actualy construction, but rather to assess whether an individual has a certain minimum level of skill.
Welding Procedure Qualification
Most fabricating codes and standards require qualification and certification of welding and brazing procedures and personnel who perform these tasks. A Welding Procedure Specification (WPS) is a document that provides in detail the required welding conditions for a specific application.
Additional Inspection Methods
In addition to the wide variety of non-destructive testing methodologies that we provide, we also offer the following inspections services.
- Welding Inspection (CWI)
- Welding Education (CWE)
- Welding Consulting
- Welding Procedures
- Inspection Consulting
- Welding Qualification
- Quality Assurance
- Quality Control
- Quality Surveys & Audits
- Steel Fabrication Inspection
- Erection Inspection
- Bolt Inspection
- ACCP Professional Level III
- ASNT NDT Level III Services
- Fireproofing Inspection
- Pull and Load Testing